How it works
Discover theRegrind Process
Collecting
The acetate that are made in the circular REGRIND process can be collected either by brands themselves; where used old eyewear or obsolete stock are turned into new raw material. Or we are collecting eyewear from organisations like Vision For All; frames that cannot be used for someone in need are being sent to us so they can go back into becoming a circular material instead.
A close the loop love act
Separation
& sorting
After the thousands of collected glasses are dismantled and sorted into different color and quality schemes, the recycling process – the regrinding – begins. This method is patented. The frames are shattered into small pieces and the metallic parts are filtered out. About 98% of the material is being recycled. The result from the regrinding is millions of small, irregular pieces of acetate - the new raw material.
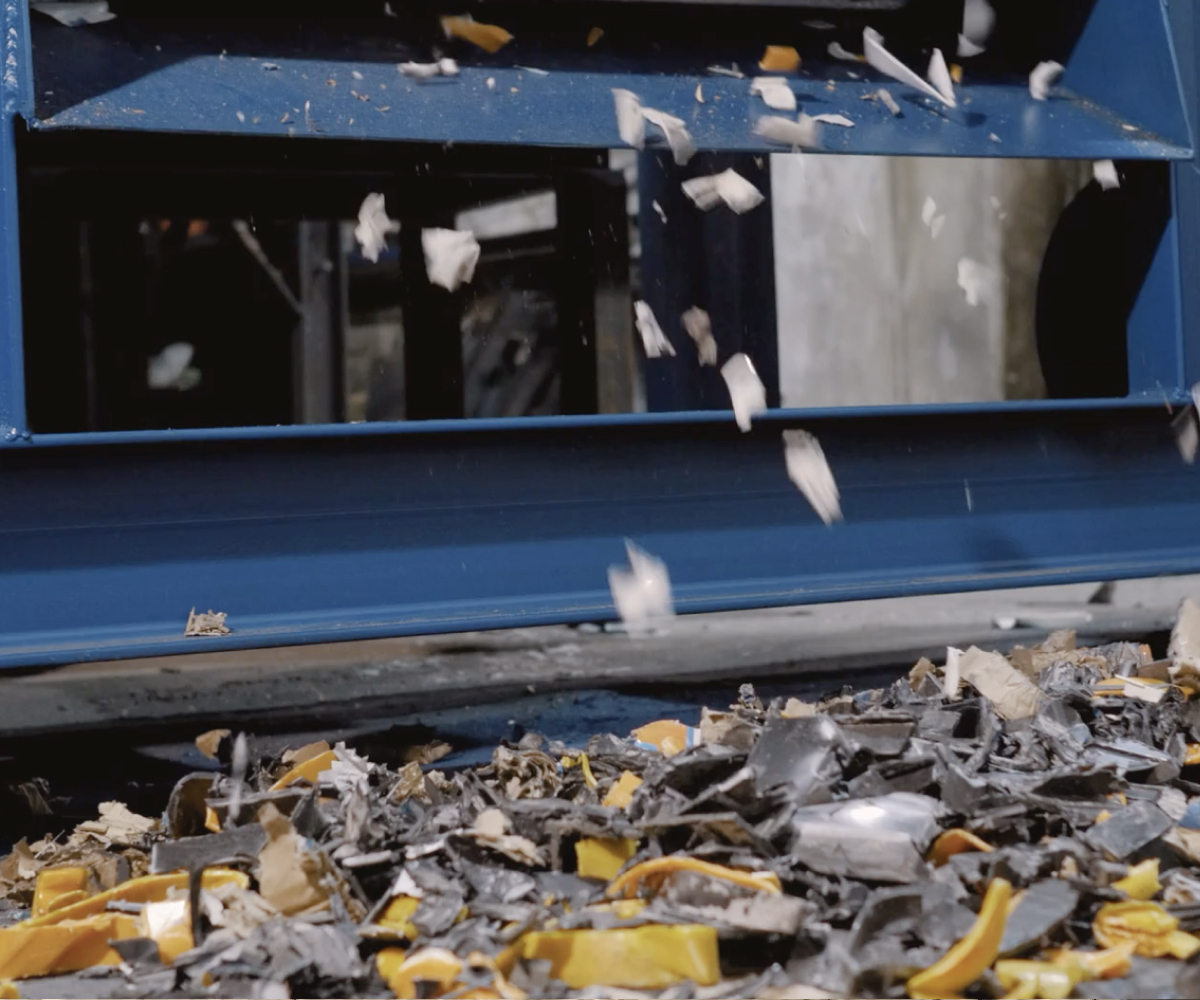
Cleaning
All the material is being cleaned to ensure future quality and for the material to be ready for the next step. Samples are taken in order to ensure that the material is 100% clean and free from metal, rubber, nickel, aluminum and titanium.
Processing
Now the material is ready to get processed into new shape and products. Turning linear into Circular.
The Regrind patented machine uses 7,5Wh per kg of material it grinds and separates.
All electricity used in the recycling process is certified to come from renewable sources and will be represented with hydro power.
New acetate
The acetate gravel is being compressed into a mold making the material a Regrind block. The material made is a patented ISCC plus certified bio-circular acetate material.
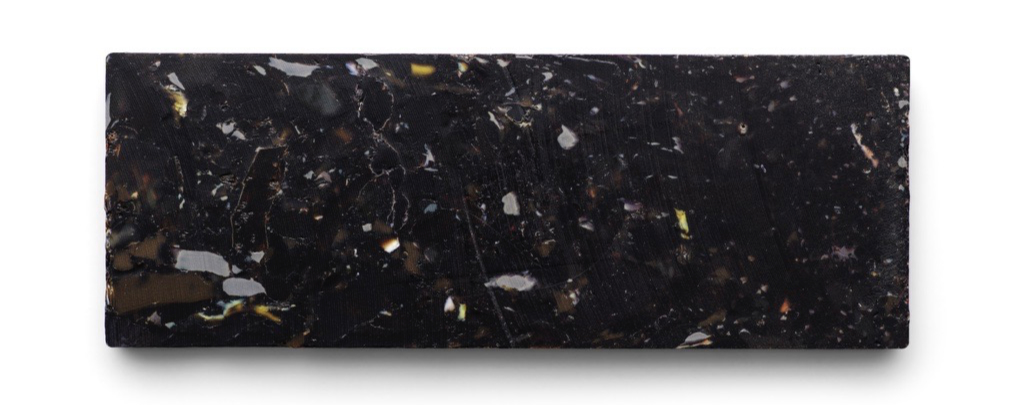
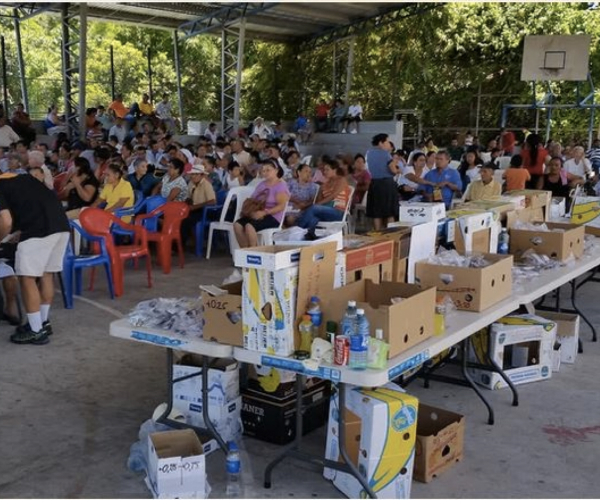
Making circular eyewear
WHAT Every year, about three billion glasses are sold all over the world. As you get yourself a pair of new ones, the old ones usually end up in a drawer or - in the best case - they are sent to a third world country. In most cases however, they end up in the trash and eventually in a landfill. Until now.
A
million pieces
HOW Collected glasses are dismantled and sorted into different color and quality schemes every month. Thereafter the recycling process – the regrinding – begins. The frames are shattered into small pieces and the metallic parts are filtered out.
About 98% is recycled.
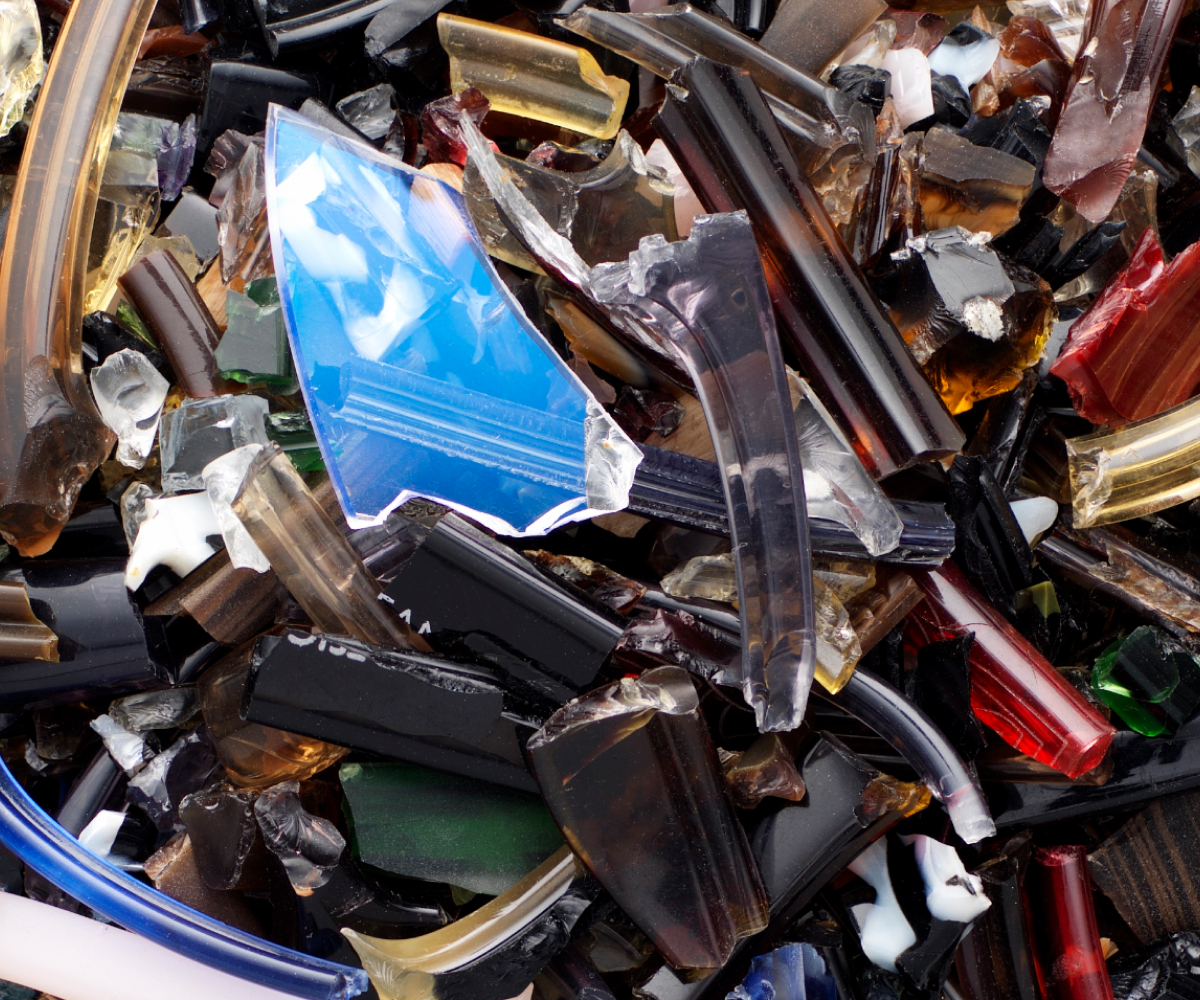
Focusing on deadstock
WHY For most of the time the dead stock is related to a few items in a collection or a line of toys that didn’t sell as expected. With this strategy larger volumes can be achieve while still having great control over the input materials, ensuring a circular favourable process.
Cleaning the world in a renewable way.
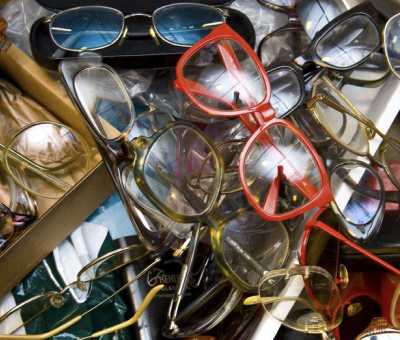
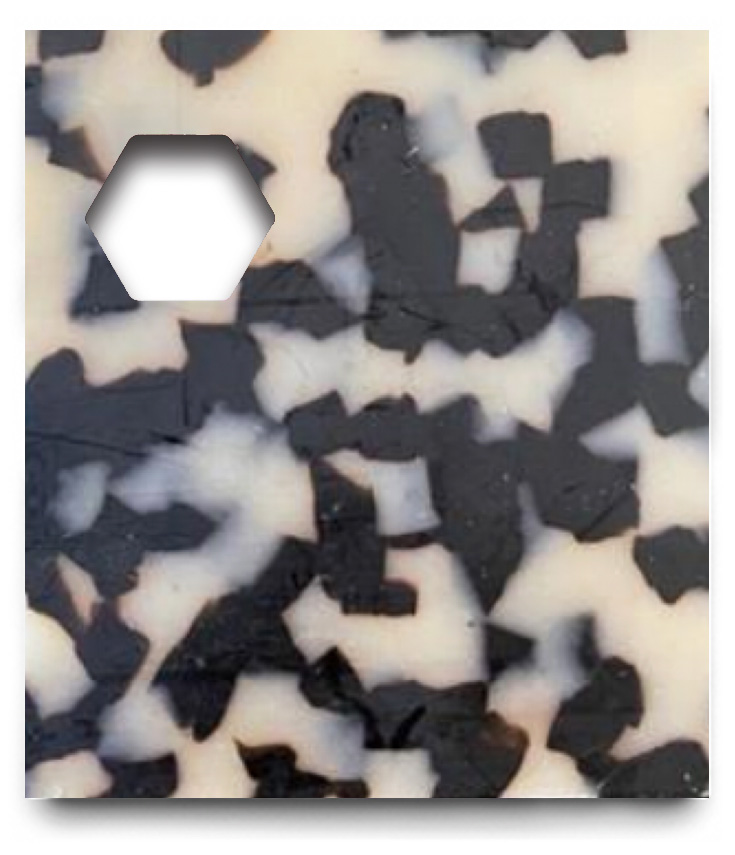
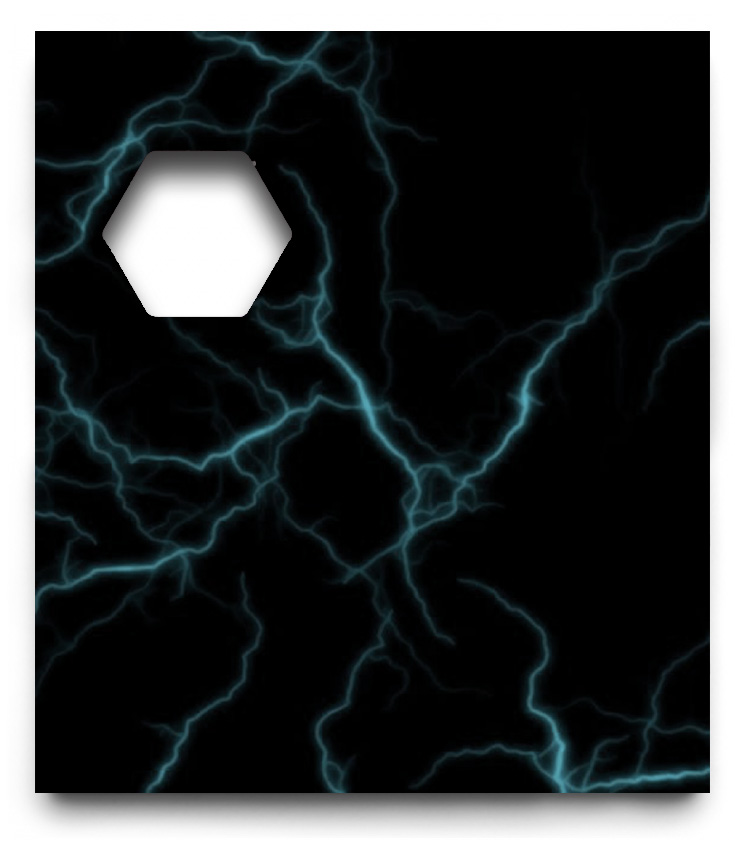
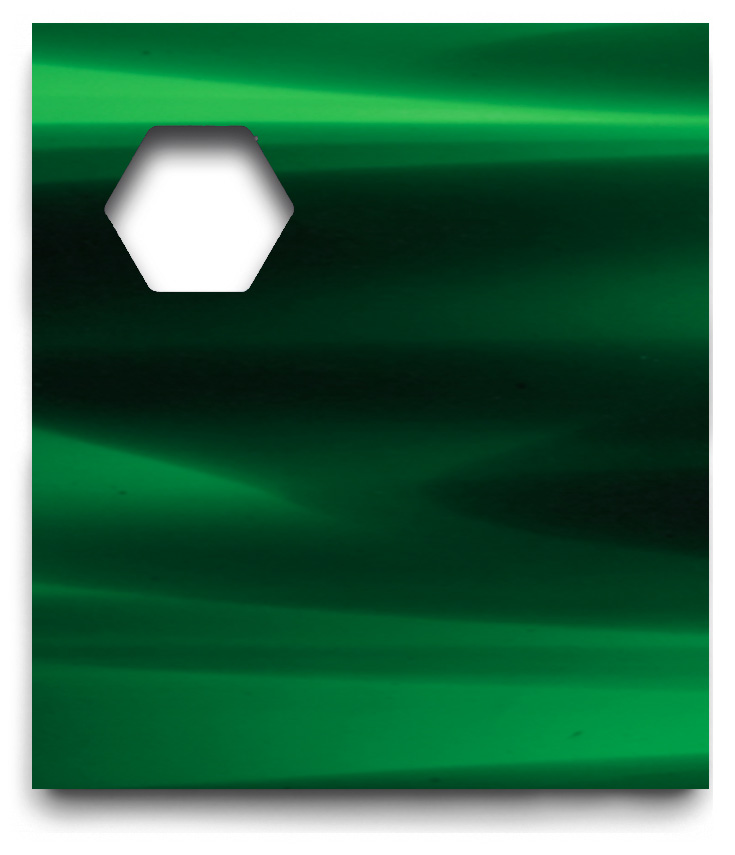
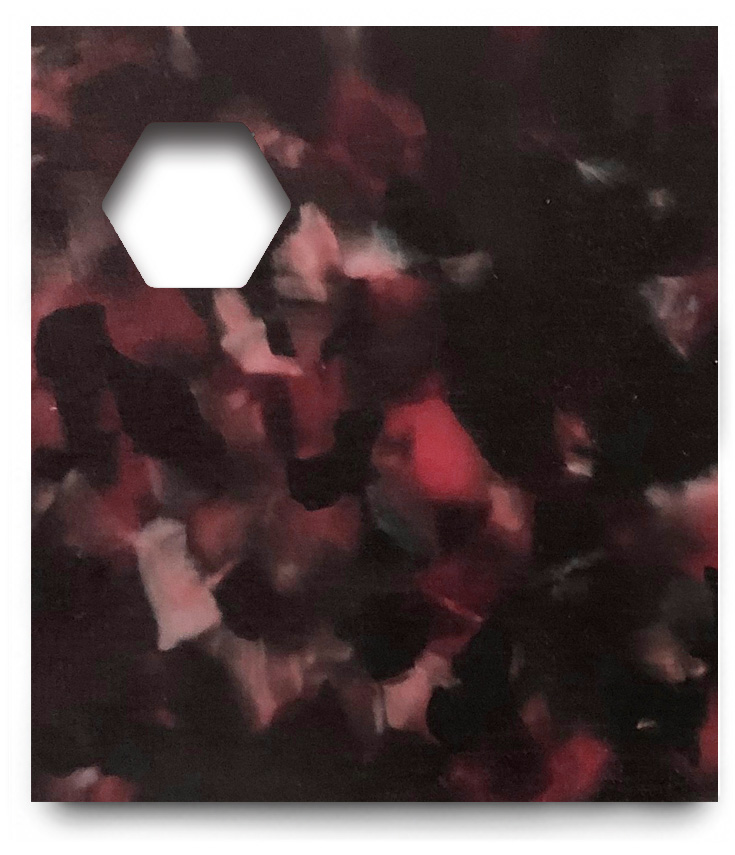
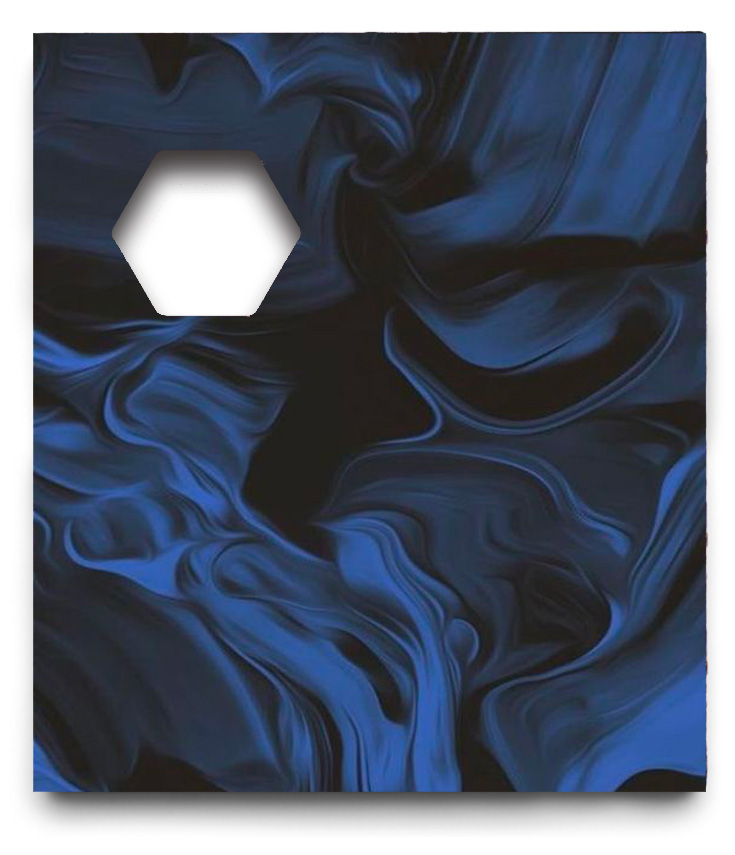
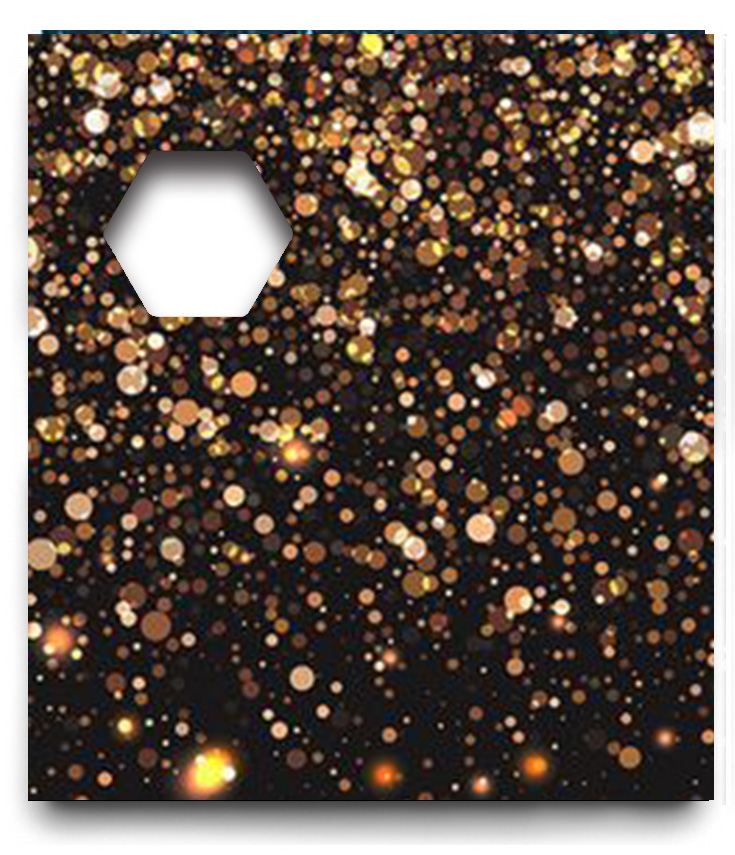
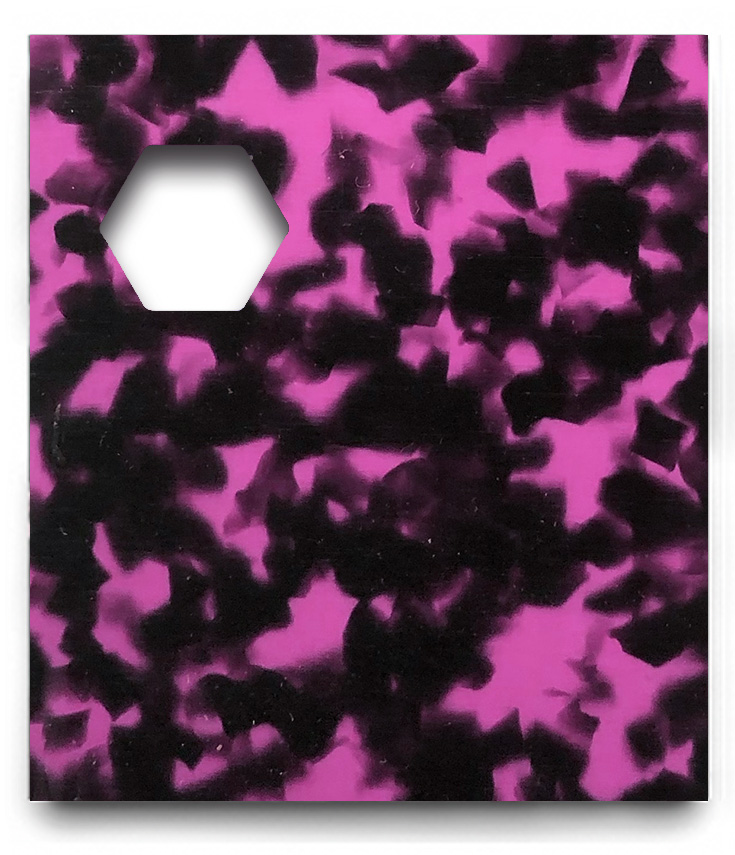
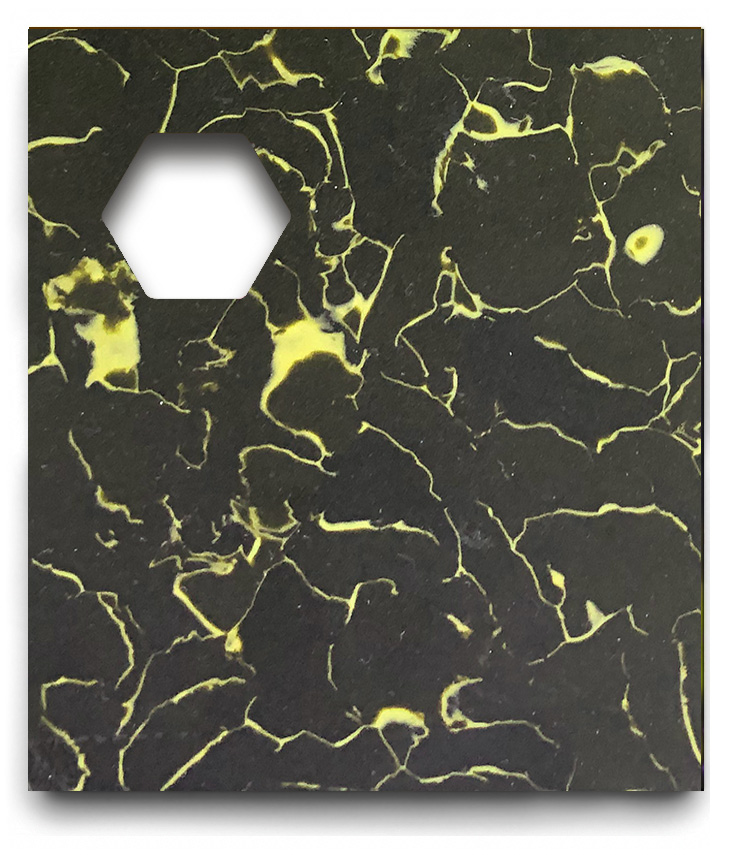
Circularity
A patented ISCC plus certified bio-circular acetate material
”This is it, what we truly are most proud of. The fact that we really are circular, we bridge the gap between just being sustainable and changing the world. Our material spares mother nature from the constant urge of usage of virgin material. Thus, saving carbon emissions but also our planet’s scarce resources”
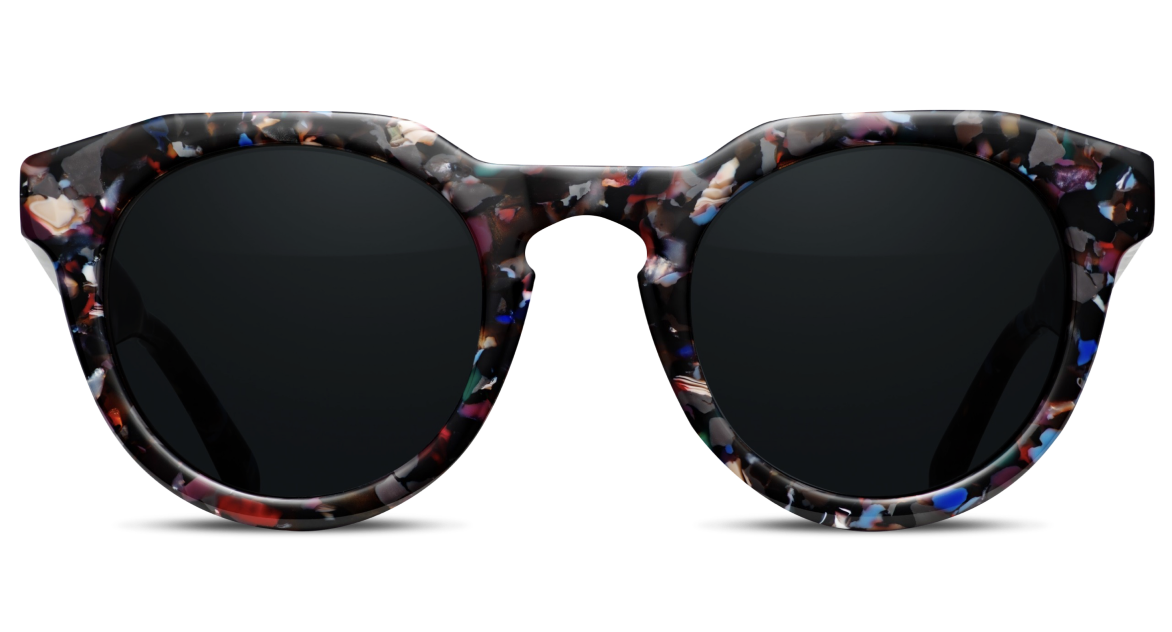
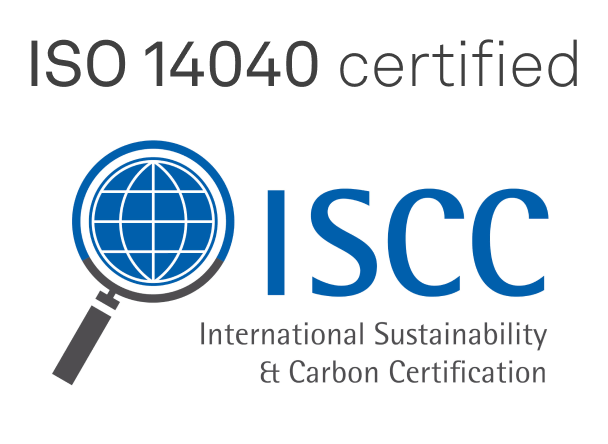
“ISCC plus helps us show transparency when making an innovative material that any brand can take part of. It has been important for us to be inclusive so everyone in the eyewear business can help focusing on being sustainable in every possible way. We are taking actions to make a positive and meaningful change both socially and environmentally around the world”-says Emilia Lindmark, Co-Founder of Regrind.
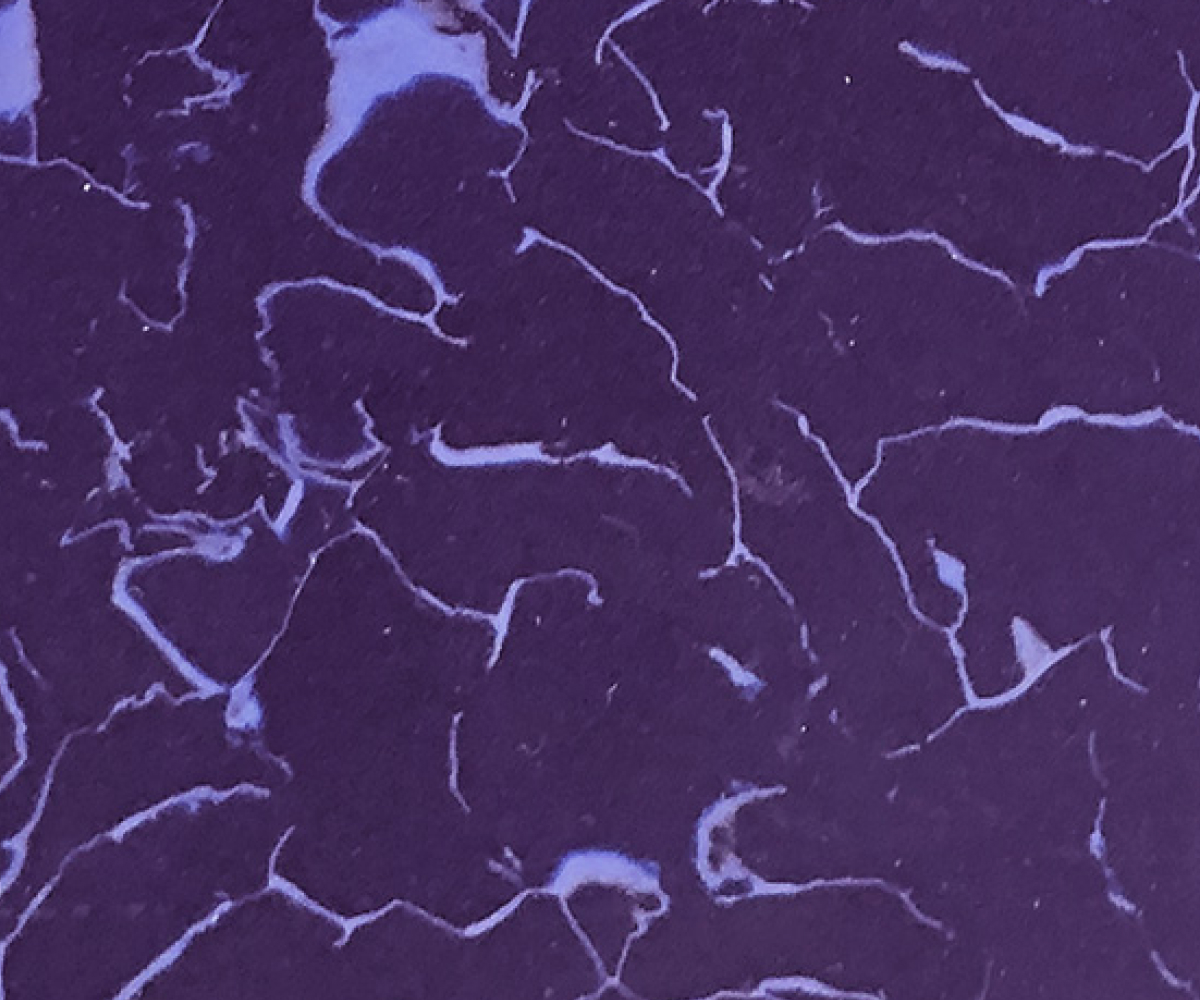